Проверка и дефектовка головки блока цилиндров
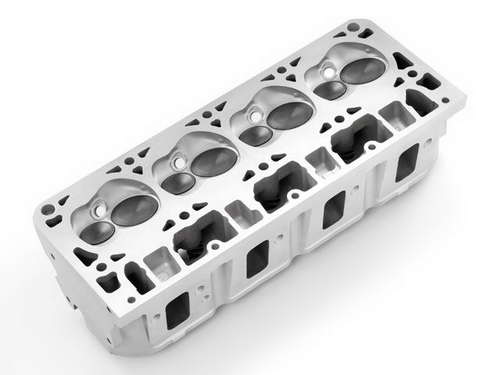
Измерительные инструменты определенного набора необходимы для того, чтобы состояние головки было проверено в полном объеме. А теперь рассмотрим, какие же размеры и параметры следует контролировать. Прежде всего, остановимся на головке, а если быть точнее, то на ее нижней поверхности. И тогда здесь просто необходим набор щупов и линейка – специальная лекальная и длина ее должна быть не менее 350 миллиметров. Далее по диагонали головки на плоскость поочередно кладут линейку, и производится подборка щупа, который проходит свободно в зазор, возникающий между плоскостью, которая образуется в средней зоне и линейкой. И величина этого зазора, так же как и наибольшая толщина подобранного щупа должна находится в пределах 0,06 миллиметров. Если же дело обстоит иным образом, то придется подвергать плоскость обработке. Хотя в повседневности даже при небольшой деформации производится обработка плоскости при выполнении профессионального ремонта. Подобная процедура затрагивает буквально все моторы - Renault, Audi, BMW и всех других автомобилей, которые можно приобрести у нас.
Также следует подвергать контролю величину изношенности подшипников кулачкового вала и опорных его шеек (если расположение вала в головке конструктивно предусмотрено). Используем микрометр, чтобы измерить диаметры шеек и нутромер для измерения отверстий в подшипнике, причем до 0,01 миллиметра должна быть точность измерения. Не более 0,10 мм должен быть зазор в подшипнике и из-за него как раз и возникает разность в полученных размерах. Соответственно, что следов износа явно выраженных, таких как задиров, всевозможных выступов или круговых канавок, не должны иметь поверхности подвергаемые контролю. При обнаружении таковых осуществляют замену распредвала и ремонтируют головку.
Необходим также контроль износа направляющих втулок и стержней клапанов. Замер диаметра стержня осуществляют непосредственно микрометром в верхней части стержня, далее уже под канавкой, предназначенной для сухарей и в конечном итоге в нижнем секторе рабочей поверхности стержня. Заметим, что по окружности замеры необходимо выполнить в нескольких точках, поскольку стержень из-за своей изношенности может иметь овальную форму. Необходима будет замена клапана, если в нижней области стержня и в его верхней области разница диаметров будет более 0,02 – 0,03 миллиметра. Необходим специальный нутромер для того чтобы определить насколько изношены направляющие втулки.
Стойка оборудованная индикатором часового типа необходима, чтобы в соответствии с люфтом нового клапана во втулке осуществить косвенную оценку изношенности. Обычно в нижней секторе втулки наблюдается наибольший износ. Если у установленного во втулку клапана измерить люфт его тарелки, то в таком случае по полученным результатам конкретно в этом месте несложно определить зазор. На таком способе измерения основаны и специальные приборы, существующие в настоящее время. Необходима замена втулки, если зазор превысил величину 0,07-0,08 миллиметра. Втулку можно и отремонтировать, но только в крайней ситуации.
В большинстве случаев визуально определяют уровень износа кулачков, толкателей, седел, коромысел и рычагов. Если приставить линейку к фаске клапана, бросив взгляд при этом на яркий свет, то можно оценить износ фасок. Клапан можно использовать вновь, после обработки, если не изношен его стержень и «провалена» только середина фаски. Также зазор с осью у коромысел не должен превышать 0,06-0,07 миллиметров, его также нужно контролировать независимо от плоскостей, которые находятся в контакте с кулачком и клапаном. Иначе после того как головка отремонтирована, двигатель будет работать также шумно, как и до ремонта.
Также визуальным осмотром определяются и всевозможные дефекты местного характера. Поскольку негерметичность соединения блока цилиндра с головкой обусловлена обычно наличием таких дефектов, как заусеницы, засечки и т.п., то состоянию головки, в частности ее поверхности, которая находится в соприкосновении с самой окантовкой прокладки надо уделить достаточное внимание. Обнаружить в стенах камеры сгорания трещины визуальным способом также иногда удается. Нагара не будет как по всей поверхности камеры сгорания, так и ее стенках непосредственно рядом с трещиной, в случае если трещина сквозная. Если подозрение все же возникает по поводу поврежденных обломками седел, клапанов стенок камеры сгорания, либо появления в ней трещин, то в таком случае необходима проверка герметичности головки перед выполнением ремонта, в противном случае ремонт может оказаться напрасным.
Мастерская не обладает специальным оборудованием, которое необходимо для организации такой проверки. Чтобы проверить герметичность блоков и головок многими зарубежными фирмами выпускаются специальные установки, однако широкого распространения у нас они еще не получили. Для того чтобы головка блока была оппрессована, необходимо все выходящие на нижнюю поверхность окна рубашки охлаждения герметично заглушить, а также находящиеся на боковых поверхностях все патрубки и фланцы и лишь один из них, через который жидкость будет поступать, следует оставить не заглушенным. Посредством воды под давлением в пределах 0,6 – 0,8 МПа, которое создается при работе специального ручного плунжерного насоса, выполняется опрессовка головки. В течение 15 – 120 минут по падению давления выявляют трещины, что проявляется наличием течи или появлением капель воды.
Существует еще одна проверка с помощью керосина, она конечно менее сложная, но для ее выполнения необходимо на седла клапанов изготовить герметичные заглушки. Перед тем как керосин наливать в подозрительную камеру, необходимо перевернуть головку вверх камерами сгорания и также ввернуть свечи в нее. Поскольку керосин имеет текучесть очень высокую, то легко проникает даже в небольшие трещины. В течение от 1 до 3 часов уменьшается уровень керосина в камере сгорания. Лучше всего заменить головку блока при обнаружении трещины.
По большому счету способы различного ремонта трещин, конечно же, существуют, но это уже отдельный разговор, но поскольку ремонтные технологии несовершенны, то отремонтированная головка все же не обеспечивает высокую надежность. Ну, вот и окончен первый этап определенных работ, которые были выполнены с головкой блока. Непосредственно можно приступить к операциям ремонтным, после того как определены практические задачи.